How Are We Doing With Machine Monitoring?
How do you monitor the performance of your shop floor? Is it effective for you?
Far from a trivial question, how to monitor performance in a production environment is an important aspect of the success of a manufacturing enterprise.
For decades, we’ve been working to identify a small number of metrics for time-sensitive data on our production that will help us make decisions and respond when changing conditions require it.
While we certainly don’t have the perfect answer that will work in every environment, here are three key lessons that can help you as you try to get answers on your production floor followed by a couple of key tools we’ve put in place to help in recent years.
1. Time-Sensitive Data is Key
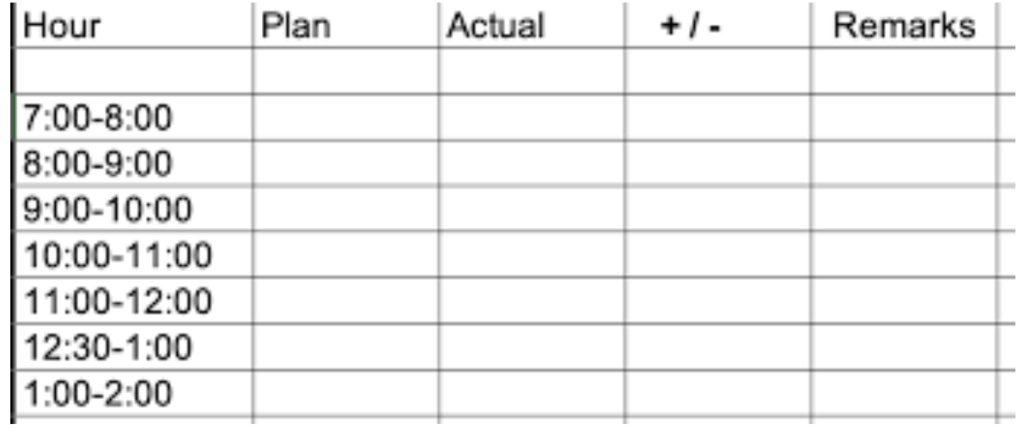
The pace of a manufacturing floor can be relentless, especially if you’re running around the clock. Data starts to become obsolete almost as soon as it’s gathered, so being able to capture and review it in a timely fashion is a huge part of making the data useful. Getting production data within a single shift has usually been in the form of Hour-by-Hour charts, or something along those lines. Those charts show current output versus expected output and can trigger you to initiate a manual signal to let your Team know when your production has fallen behind. The consistency of the operator to work the chart and request assistance is key to having this method prove effective.
2. Data Acquisition without Human Interaction is a Key Opportunity
As humans, we struggle to be consistent in most anything. That’s certainly the case on the shop floor. Taking the time to collect data, make sure it’s accurate (even when it may show you’re not performing as well as expected!), and report it (so that the folks higher up in the organization can see how you’re doing) isn’t exactly the exciting part of the job. Even reporting at the end of a shift is subject to the time, effort, and energy you’re putting forth to report results. In recent years, there are many technology tools to help monitor machines that don’t require human interaction. Making use of one of these tools can provide a consistency of data that wasn’t typical until recently. We’ve learned that automatically generated data, while not perfect, can provide a foundational component to an improved data set without taxing your Team. One big benefit of getting data without human effort is the consistency available without adding burden to already busy shop floor personnel.
3. Do a Historical Review to See Trends
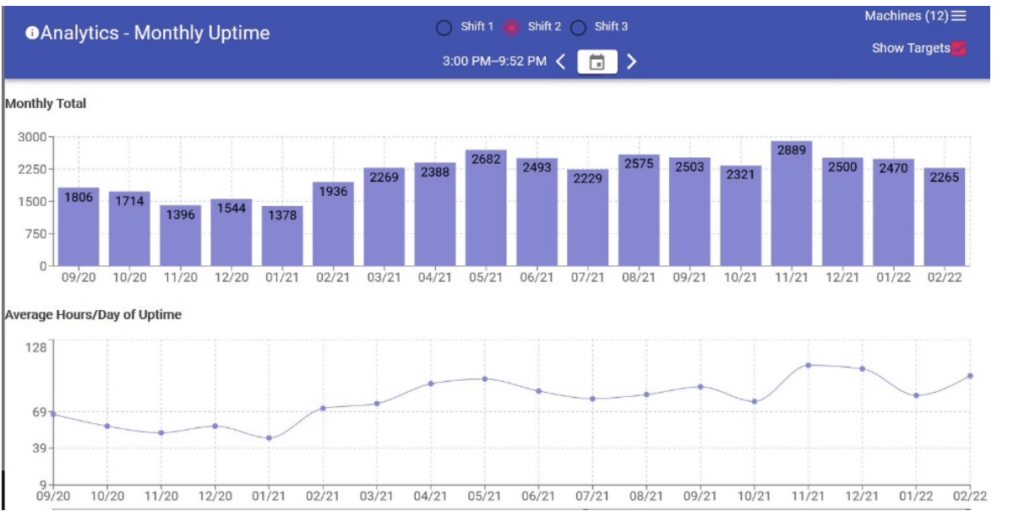
While time-sensitive data is important to help make decisions during a shift or day, there is also value to stepping back to review longer-term production data to see trends. Recognizing there are a tremendous number of variables in almost any shop environment, you can still learn from data accumulated over weeks and months. It’s not easy to account for all the variables, but data trends over time on the shop floor can help you make bigger decisions regarding staffing, new machine acquisition, and product mix. Recording data for easy review can be complicated, and the extra work may or may not seem worthwhile, especially in a busy environment that continues to move forward at a relentless pace.
There are two main tools that we’ve used in recent years to help provide better monitoring of our shop floor production.
1. Google Sheets
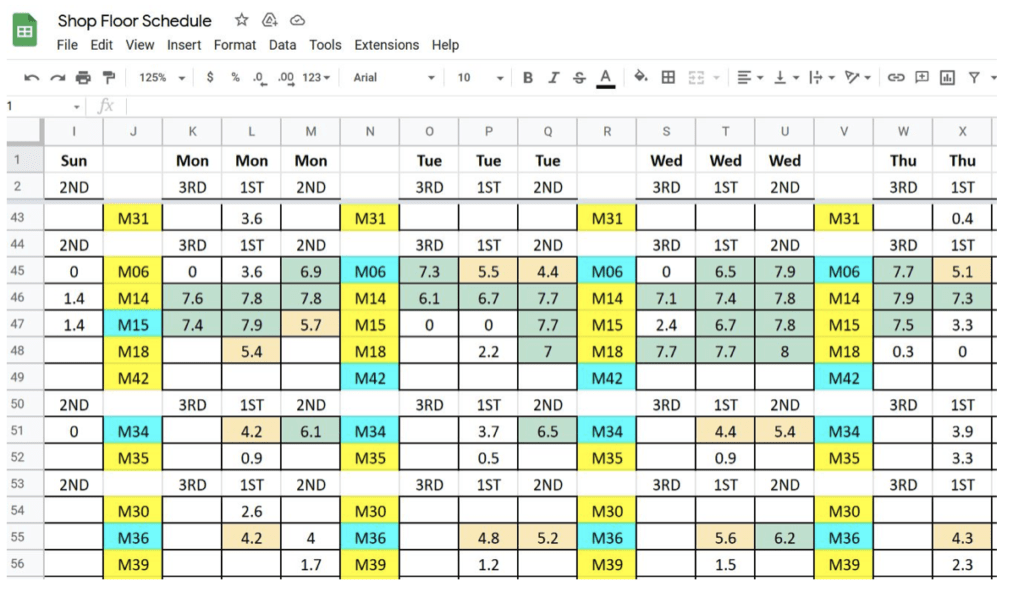
Hour-by-hour charts and other manual performance monitoring can be greatly enhanced by the use of Google Sheets, simply because the data can be written and viewed from multiple locations simultaneously. Excel has been a popular tool in the past for a variety of functions, especially in smaller shops where purchasing shop floor management software isn’t cost-effective. Expanding the capability of Excel by taking advantage of the Google Sheets platform adds significant versatility and usefulness to the data collection. Viewing becomes possible from almost anywhere, including from a smartphone. While still dependent on the consistency and accuracy of the human inputs, it can be a very helpful option to share information across your company
2. Machine Utilization Tracking System
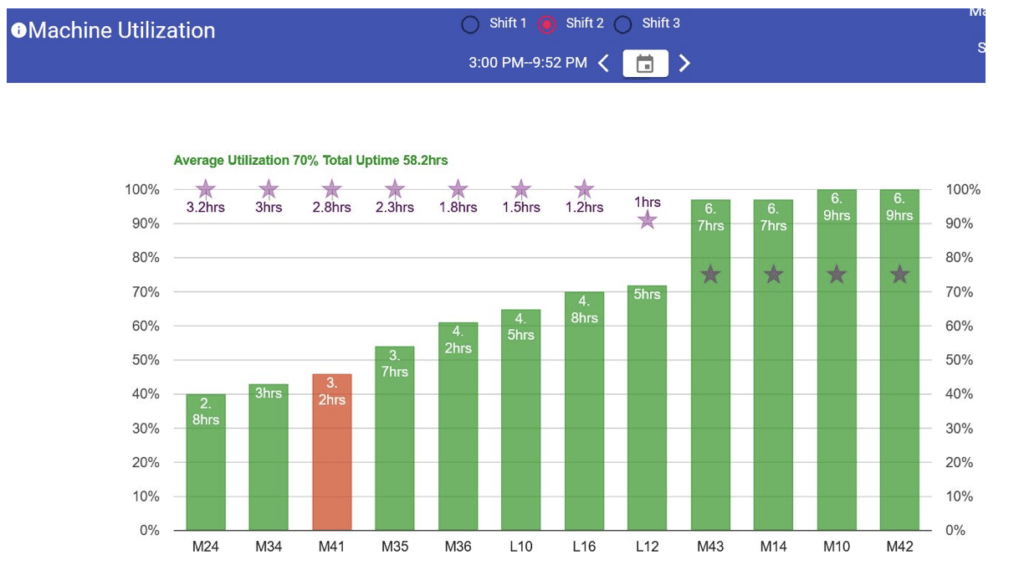
A few years back, we adopted a system for monitoring our machines that measures the electrical current flow powering the machines. In operation, the machines draw dramatically more current than when idle, so it’s pretty easy to sense when they are running. Transmitting the data through a WiFi connection to the cloud, the data is both real-time and automatic. Monitors on the shop floor show the Team the status of the machines and can provide obvious visual cues throughout any shift on the performance of each machine. Because the data presentation is cloud-based, it can be reached anywhere from an internet browser. Additionally, the software package provides for historical data evaluation, trend analysis, and plenty of comparisons. While there are limitations to the data set captured in this manner (i.e. lack of differentiation between good parts and bad parts, no setup time evaluation or comparison, etc.) it’s still a tremendous tool for production monitoring and checks most of the critical boxes for our use.
Final Thoughts
Knowing how well your shop is performing is a long-sought-after measuring criterion.
While there aren’t any perfect answers, hopefully, some of these ideas can help you improve your data collection and the resulting decision-making for your business.
If you’d like to speak with someone who knows how to make production monitoring easier, check out Machine Tracking or contact us.