Cobots in Manufacturing by Andrew McCartney, Updated for 2024
In celebration of our continued commitment to Industry 4.0, recognized when receiving MAGNET’s Northeast Ohio Manufacturing Lighthouse Award this past year, we’re excited to share our ongoing journey with Collaborative Robots, commonly known as Cobots.
A Look Back: Our Initial Robot Experience
In the early 2000s, we ventured into automation by acquiring a used Fanuc robot for $12,000 to aid in machine-tending tasks. Despite the promising potential, integrating the robot electrically with our machine tools presented significant challenges. We invested an additional $10,000 in hiring a team to help us with the setup. However, persistent electrical issues led to multiple failures of the Input/Output (I/O) boards in our Haas machine, ultimately forcing us to abandon the project. The robot was subsequently donated to a local trade school, a testament to our belief in its potential, despite the technical hurdles we couldn’t overcome.
Transition to Cobots: A New Era
Fast forward to 2018, we identified another opportunity where automation could significantly improve our processes. We were managing high demand for a part requiring both lathe and mill operations, handled by two Teammates across two lathes and one mill. We believed a Cobot could streamline this process and free our Teammates to focus on more complex tasks.

The key differences between traditional robots and Cobots are noteworthy:
- Safety and Collaboration: Traditional robots required extensive safety fencing due to their speed and potential danger to humans. Cobots, designed to work alongside humans, come with built-in safety features that halt their motion upon encountering unexpected obstacles.
- Simplicity in Integration: Cobots don’t require complex electrical integrations with machine tools. Instead, they mimic human actions, such as pressing a start button, which makes Cobots easier to implement and operate.
We opted to lease a Cobot to test its viability in our operations. The Cobot, though more expensive than our initial robot, promised easier integration and greater flexibility.
The Reality of Cobot Programming
Our young engineers were eager to get the Cobot operational. Initial programming seemed straightforward, and within an hour, they had created a few hundred lines of code. However, as we delved deeper, our Team realized there was significantly more complexity involved in programming Cobots successfully. While basic motions were quickly set up, the detailed programming for tasks like loading, unloading, and machine activation was far more intricate. The final program spanned several thousand lines of code needed to cover all potential edge cases and exceptions.
Our Production Challenge
Deploying the Cobot into production also revealed significant issues. The Cobot’s cycle included tasks such as unloading parts from the lathe, blowing out the lathe chuck, loading new parts, and starting the machine. However, the proximity of the lathe and mill, necessitated by the Cobot’s limited arm length, created challenges if even one part of the process went wrong.
Our older machines, particularly the lathe, frequently experienced issues that halted operations. While our engineering team could quickly resolve these during the First Shift, we lacked similar expertise on the Second and Third Shifts, which led to production stoppages. Our options were limited: either let the system sit idle until the next shift or manually override the Cobot to keep production running. Both options were inefficient.
Despite numerous attempts to rectify these issues, we concluded that our machine tools were simply too old to continue the project. We removed the Cobot from the cell and reverted to manual operations. Ultimately, we solved that challenge by investing in a live-axis lathe that could handle both operations in a single process and removed the need for Cobot loading altogether.
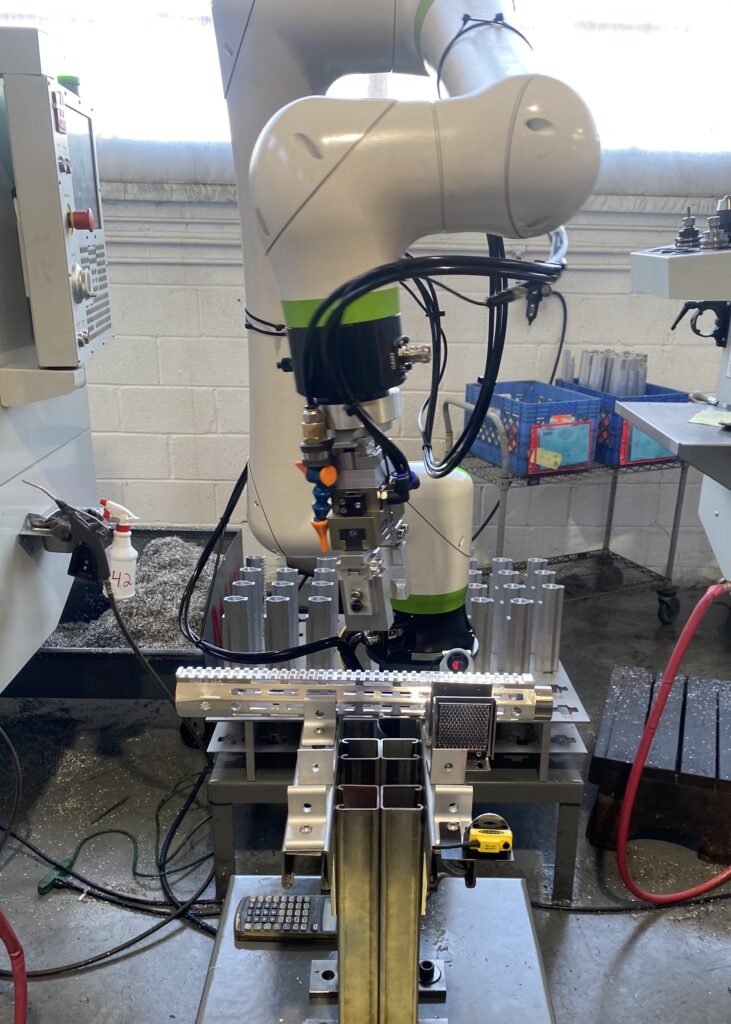
Finally, Successful Integration!
In July of 2023, we made another attempt to integrate a Cobot with our machine tools, and this time we achieved success. Learning from our prior experience, we paired the Cobot with two of our newest machines, so we weren’t limited by over-running older machines.
With the help of Absolute Machine Tool, coordinated with some grant money from MAGNET, we were able to get tooled up and successfully into production on one of our extruded aluminum product lines. This family of products has a common loading methodology that has allowed us to run a variety of similar part numbers with limited change-over time in between.
One of the limiting factors for using a Cobot is how many parts are needed to run. The greater the number of parts to run improves the opportunity to get a return on that investment of time, energy, and resources. In the case of this product line, we were able to run a variety of parts for nearly a year before we outpaced the market demand and had to take a break from running.
Still, it was great to have a successful integration, and we’re already looking at the next family of products to run through a cell with a Cobot loading and unloading the machines.
Looking Forward: A Time-Out, Not a Retreat
While we tapped out the market potential in our most recent application, we were grateful for the lessons that we learned during the eleven months we ran our Cobot cell, and we’re excited for the next opportunity. There’s no question that keeping a cell running around the clock has extreme value for our business. In addition, we gained valuable insights and learning opportunities that will serve us as we continue our automation journey. We certainly plan to revisit using Cobots to load the next product family on more of our newer machines.
Cobots represent a critical aspect of Industry 4.0, and their role in manufacturing will only grow. We are excited about future opportunities and are committed to finding the right applications to leverage their potential effectively.
Final Thoughts
Our journey with Cobots has been challenging but enlightening. We are more determined than ever to integrate advanced automation in our manufacturing processes. As we explore new product families that could be automated and better ways to facilitate the loading, unloading, and change-over between parts, we aim to harness the full potential of Cobots, driving efficiency and innovation in our operations.
Check out THIS video of Bowden Manufacturing’s cobot in action as it seamlessly handles machine tending tasks.
Stay tuned as we continue to explore and embrace the advancements in Industry 4.0 technology, paving the way for a more automated and efficient future in manufacturing.