How Do You Measure Productivity and Utilization?
It’s an age-old challenge in manufacturing plants – How do we measure productivity and utilization?
If you’re like most folks, you’ve tried all sorts of different methods. Unfortunately, most methods rely heavily on human interaction, typically in the form of reporting pieces, hours, or machine cycles.
A system requiring human interaction means that the data is only as good as the reporting and human nature isn’t typically working on your side. Most people don’t want extra tasks, and they certainly don’t want to have to report potentially negative information about their own performance. That can definitely limit the effectiveness of the system.
Machine Utilization Trackers
After many years of experimenting with several different methods of recording and displaying a variety of data to help drive productivity and utilization, we found out about a new Industry 4.0 option in the marketplace. The Machine Utilization Tracking (MUT) System was a cost-effective means of collecting and displaying the uptime and usage of our machines. Best of all, it doesn’t require any human interaction for data collection or display!
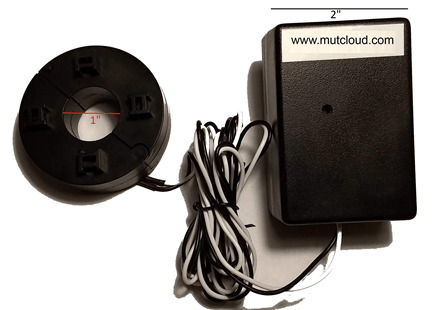
The output of the system is a web-based browser view that shows all the machines and the real-time status for each. Clear visibility from anywhere you’ve got an internet connection.
Machine Utilization Tracker Results
Before we started using the MUT System, our productivity was pretty typical for smaller machine shops that have a wide variety of job-shop work. On average, we were in the 40-45% utilization on our machines. Many factors influenced those numbers -the type, quantity, and cycle time of the jobs were the biggest- but over time the trends become obvious to see.
After we got all of our machines onto the MUT System, we started seeing an increase up in the 60-80% range on a regular basis. Awareness and visibility clearly drive behavior. Our Team has always wanted to do a good job, but having the data created awareness that helped drive greater productivity.
The Next Level – Setting Targets
As we experimented with different ways to help our Team utilize the data, we worked with the Machine Tracker Team to add specific Targets to each machine for each shift. We wanted to do it so that it would require a minimum of human interaction… max 1 or 2 times per shift by the Team Leader.
The resulting tabular format makes it easy to see how we’re doing at any given time during a shift. Not all machines have clear productivity expectations on a given shift… .especially during setups or under limited staffing conditions. Machines for which we could identify a target, the MUT System displayed real-time progress towards the goal. The resulting visual representation of progress provides data that was previously difficult to see in anything short of an hour-by-hour chart.
Setting Targets Results
Adding the Targets to our MUT System display has resulted in an additional 10-15% increase in productivity and utilization. It also draws immediate attention to machines that have fallen behind early in a Shift, so that Team Leaders and take early action to help get things back on track.
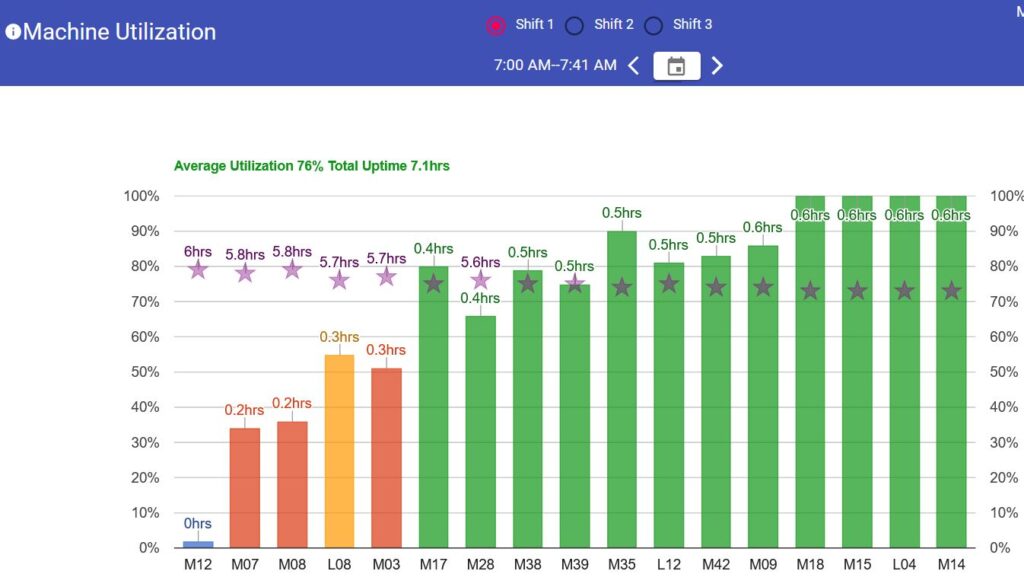
Countdown Timers
As we’ve encouraged our Team to work together on the shop floor, we’ve looked for a way to help our Team anticipate when a machine will complete its cycle. If it were obvious which machine in a particular group would be the next to finish, wouldn’t that help us ensure we had a Teammate ready to unload the completed part and reload the machine with the next blank? We refer to it as having a “Hand on the Door” when the cycle ends, so that we’ll minimize downtime after the machine completes a cycle.
The Machine Tracker Team helped design the Countdown Timer System so that it was another system to provide highly visual, real-time data for our Team that required limited human interaction for it to work. By adding another small sensor to the machine tool, using an installed relay, and adding a few lines of code to the machining program, the Countdown Timer System had what it needed. The result was an easy-to-see and use screen showing the machines running in a group, and the countdown until their cycle will be completed.
The start of a new cycle resets the timer and it counts down with a green background. With 1 minute to go, the timer background turns yellow to alert the Team. Once the countdown is complete, the timer background turns red and stays at 0:00 until the cycle is restarted.
Countdown Timer Results
As we expected, when the timers are being used, the added visibility increases productivity and utilization. The typical increase is another 10-15% over just having targets and routinely results in 80%+ machine utilization. Additionally, the cultural impact of helping promote Teamwork and visibility is an added benefit.
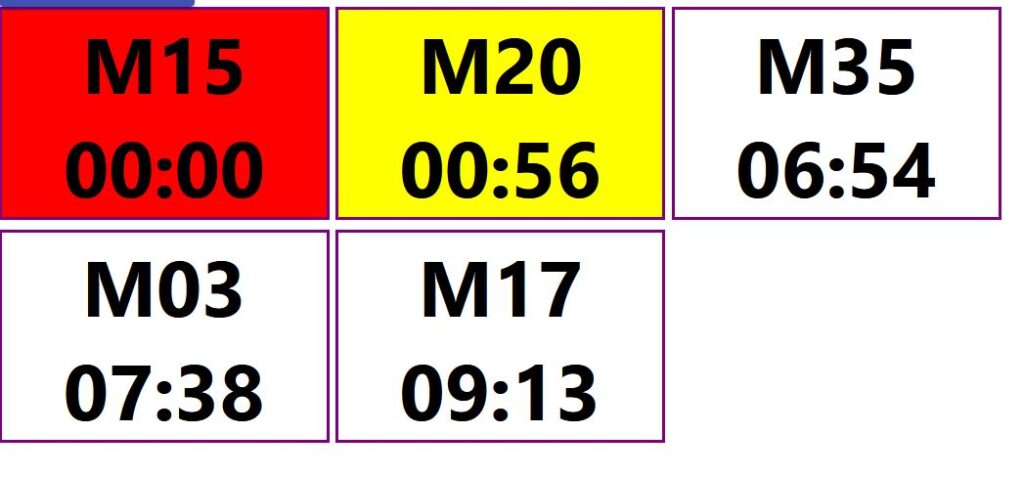
You Can Do It Too!
Unlike many of the Industry 4.0 solutions that we’ve seen presented, the MUT System and Countdown Timer Systems have two big advantages: They are very affordable and very easy to install.
The MUT System works for any piece of electrical equipment, regardless of age or technology. It installs in seconds and only requires a web browser to see the data output. Inputting production targets is done in a simple spreadsheet, that is updated as needed. It couldn’t be much simpler.
The Countdown Timer System takes a small amount more to install, but it’s still quite simple. We have a large group of Haas machine tools that come standard with 4 additional, unused relays that can be activated by the machine programs to signal the start and stop of the machine cycle.
We have several other brands of machine tools and worked with the Machine Tracker Team and a Team from MAGNET to get them up and running. Our TongTai machine tools allowed for additional relays to be installed very cost-effectively. For our Mazak and Mori Seiki machine tools, we found a mechanical solution that has wider opportunities to be used for almost any machine. By installing a physical switch that the machine can activate at the start and end of the cycle, the solution doesn’t require a special electrical interface with the machine tool. Sometimes the simplest solution works the best!
Want to Learn More?
If you’re interested in learning more, we’re happy to share our experience to help you start your Industry 4.0 experience. You can contact us, the Machine Tracker Team, or the folks at MAGNET to learn more. Hopefully, you’ll embrace the opportunities of new technologies as they emerge to help you grow in productivity and utilization throughout your manufacturing environment.